Green Electronics - Environmentally Responsible Alternatives to Traditional PCB Fabrication
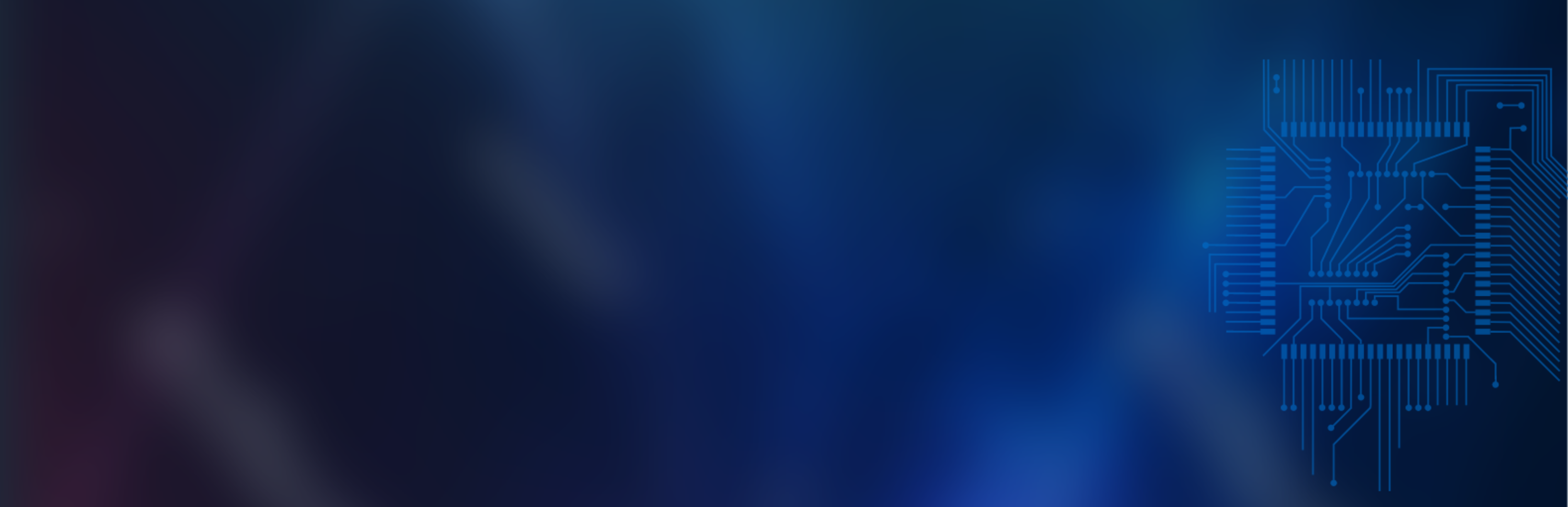
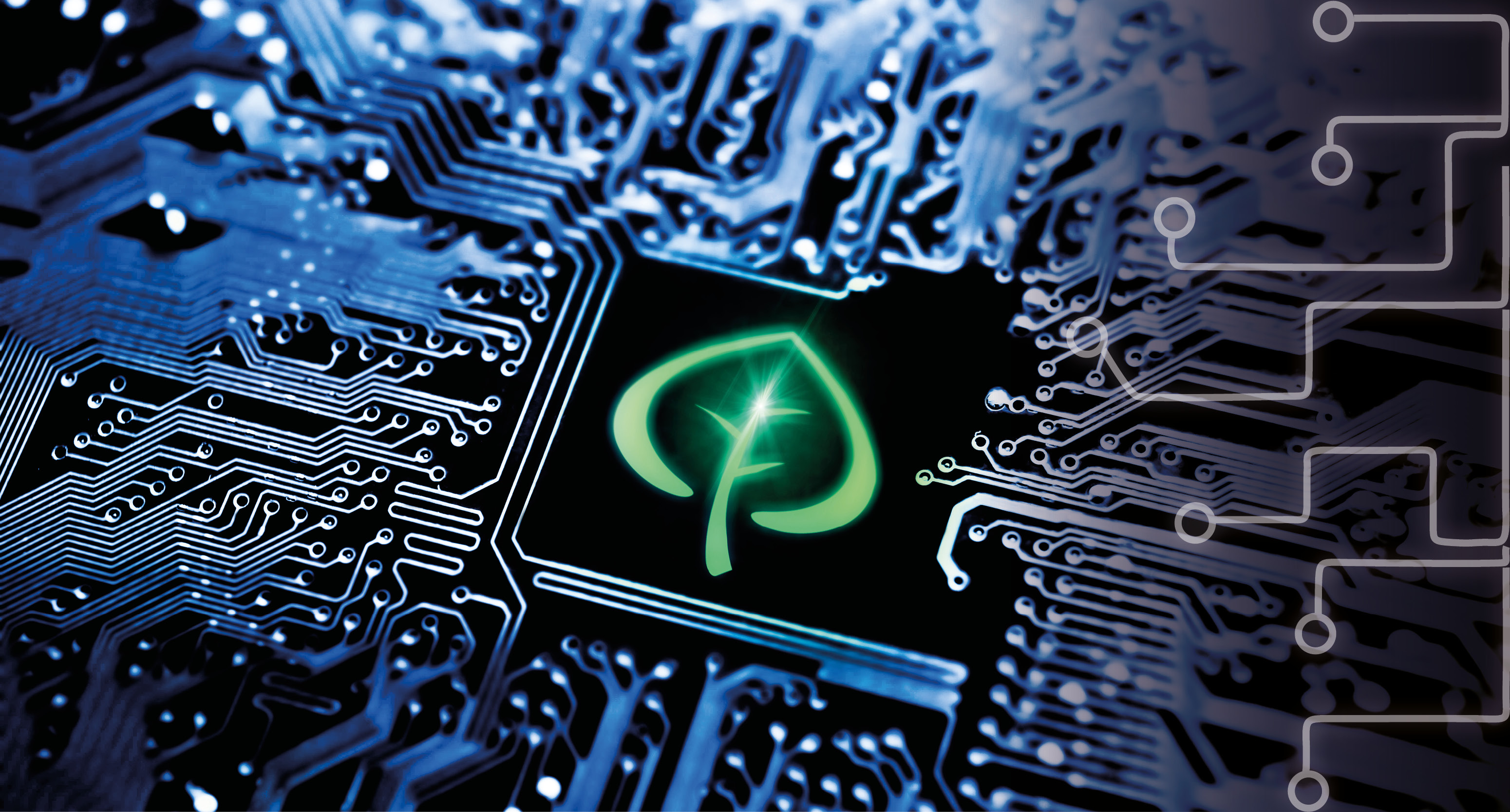
Written By
Mark Edwards
Strategic Account Manager
Circuitry Solutions
MacDermid Alpha Electronics Solutions
Want to speak to an expert? Connect with us here:
Green Electronics - Environmentally Responsible Alternatives to Traditional PCB Fabrication
The electronics industry is one of the largest economic sectors in the world and I am glad to be part of it. Since its emergence in the early 20th century, it has grown into a multibillion-dollar industry. The global printed circuit board (PCB) market was valued at $82 billion USD in 2022, and Precedence Research predicts this to expand to $140 billion by 2032.
A key factor driving growth in the PCB industry is the rapidly increasing demand for smart electronic devices. From smartphones, tablets, and medical wearables, to industrial, military and aerospace applications, smart electronics are providing increased control, productivity, and convenience that the world has become increasingly dependent upon. Today’s electronics are vital to many aspects of modern society. They are at the heart of sophisticated systems that enable modern communications, national security, vehicle safety, electronic banking, military, and defense systems, and so much more.
Environmental Impact of PCB Fabrication
Despite their countless benefits, electronic devices have spawned challenges and concerns. One of the biggest concerns, is in my opinion, the impact PCB fabrication has had on the environment. Traditional methods of fabricating circuit boards are energy-intensive, use hazardous chemicals, and consume substantial amounts of water.
Creating conductive electrical pathways within a circuit board is an integral part of fabricating PCBs. Traditionally this process has relied on a chemical process called electroless copper plating for primary metallization. This process requires PCBs to be immersed multiple times in chemical baths that contain cleaners, catalysts, cupric salts, reducing agents (usually formaldehyde), activators, and substantial amounts of water. Additionally, chelating agents, like EDTA, are needed to control process stability, and a variety of stabilizers are used to prevent undesired characteristics like rough deposits and coarse grain structure. Many of these chemicals are considered hazardous and need to be removed through wastewater treatment. Unfortunately, some are not easily removed from solution and are resistant to conventional wastewater treatment procedures.
With increasing pressure by regulatory agencies, it seems odd that commercial electroless copper processes still utilize formaldehyde as the reducing agent, given the known health risks associated with formaldehyde exposure. While there are no bans on formaldehyde in the electronics industry, many countries have put forward regulations on the amount of annual importation or manufacturing of this chemical.
Also eye-opening is the continued usage of EDTA as the chelator in the electroless copper process. There are increasing legislative efforts in Germany and Japan to stop the use of EDTA since it is known to draw potentially toxic metals into the wastewater stream.
These pollutants, if not properly treated, pose significant risks to water quality and the health of aquatic ecosystems. Furthermore, the large amount of energy consumed during electroless copper plating contributes to greenhouse gas emissions, which according to the IPCC (Intergovernmental Panel on Climate Change) are contributing to global warming and climate change.
Direct Metallization – An Environmentally-friendly Alternative to Electroless Copper Plating
Fortunately, chemists and engineers working at universities and environmentally responsible corporations have been developing alternatives to electroless copper plating.
I am pleased to say that environmentally preferable technologies, like direct metallization, continue to gain traction in the PCB industry. Direct metallization alternatives eliminate formaldehyde, EDTA and other hazardous chemicals while significantly reducing water and energy consumption. Combined, these factors dramatically reduce the environmental impact of a critical step within the PCB fabrication processes.
Direct metallization is an innovative technology transforming the way conductive electrical pathways are fabricated within PCBs. Hundreds of manufacturers have already approved and transitioned from electroless copper plating to direct metallization for making simple and complex circuit boards, from flexible, rigid-flex and hybrid constructions to multi-layer PCBs with high-density interconnections (HDI).
Several PCB manufacturers were interviewed after their transition to direct metallization as part of the Design for the Environment Program funded by the US Environmental Protection Agency (EPA). Real-world performance data collected in the program confirms that direct metallization performs as well or better than traditional electroless copper plating and offers the following advantages.
Transitioning from Electroless Copper Plating to Direct Metallization provided:
-
Significantly shorter cycle times, allowing PCB fabricators to quickly turn their jobs.
-
Improved hole wall reliability, even for small holes and microvias.
-
Direct copper-to-copper bonding and epitaxial grain structure.
-
Fewer defects, like micro voids, for improved reliability.
-
Improved quality, reducing the need for visual inspections.
-
Elimination of acid cleaners, scrubbers, formaldehyde and EDTA.
-
Dramatic reduction of chemical and water usage.
-
Lowered expenses related to wastewater treatment.
-
Decreased chemical, labor, and maintenance costs.
-
Automated process features for improved efficiency.
-
Reduced occupational hazards.
-
A means to help customers meet their corporate sustainability objectives.
With the potential to improve quality, streamline manufacturing, control costs, and minimize the environmental impact, direct metallization is a promising technology for creating conductive electronic pathways within printed circuit boards.
Navigating Risk Management when Transitioning to Greener Technology
Environmental stewardship is a choice, and I understand it is a big decision to research, evaluate and change to a different technology. However, by sharing information and working together we can successfully navigate the risks and reap the benefits going forward. Lean on experts, like MacDermid Alpha, with over four decades of expertise in direct metallization. MacDermid Alpha has helped global PCB fabricators adopt direct metallization technologies instead of the electroless copper process and they can help you too!
Interested in transitioning to direct metallization?
Talk to our experts here and we'll help you take the first step