Enhancing Safety, Reliability, and Efficiency of Onboard Chargers with Integrated Electronic Assembly Solutions
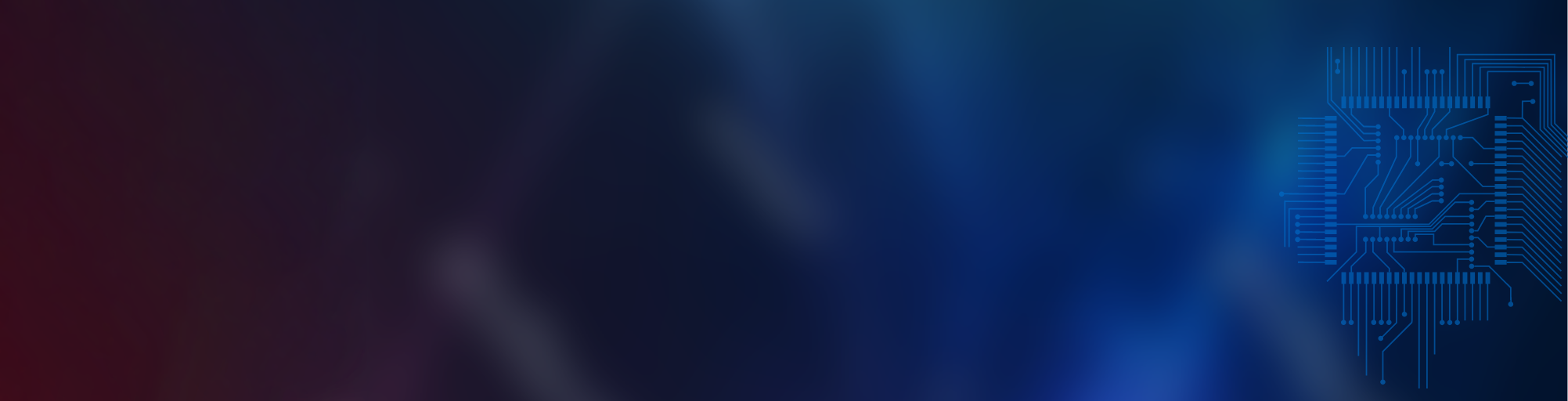
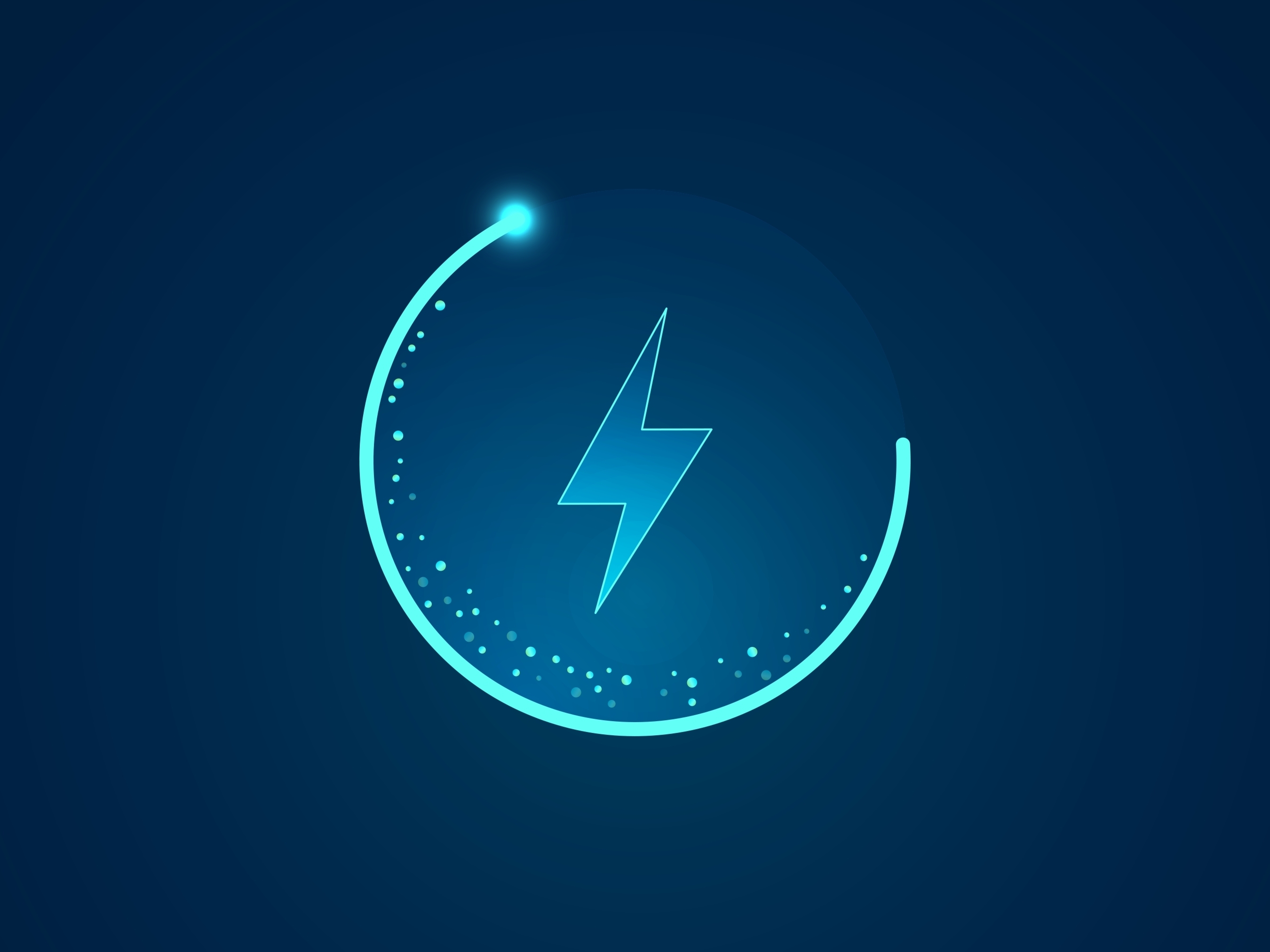
Challenges for Automotive Electronics
The onboard charger (OBC) is a vital component of an electric vehicle (EV), enabling the safe and efficient conversion of AC power from charging stations to the DC power required to recharge the battery. Beyond power conversion, the OBC acts as a critical hub for communication and control, interfacing with the vehicle’s controller and the charging station. By monitoring and optimizing charging parameters like voltage and current, the OBC ensures the battery is protected from risks such as overcharging, overheating and other electrical faults, thereby contributing to the safety and longevity of the EV.
As demand for EVs surges, advancements in technology are accelerating at an unprecedented pace. However, this rapid progress brings a host of challenges for sensitive automotive electronics, which must endure a wide range of operational and environmental stresses, including extreme temperature fluctuations, mechanical shocks, vibrations, drop impacts, and exposure to moisture, dust, dirt, and chemicals.
Compounding these challenges is the growing need for faster EV charging. Rapid charging requires either higher voltage or increased current. While increasing current accelerates charging, it also leads to greater energy losses and heat generation, making the process less efficient. To address this, superchargers are adopting high-voltage solutions to deliver power more quickly and efficiently.
Integrated Solutions for High Voltage OBCs
This transition to high-voltage superchargers intensifies the stresses on OBC electronics, highlighting the critical need for enhanced durability and reliability. In response, EV manufacturers are reengineering in-vehicle OBC electronic assemblies to ensure safe and dependable performance in high-voltage charging environments.
This article explores five advanced electronic assembly solutions that meet the growing safety, and reliability demands of OBC electronics, paving the way for next-generation rapid EV charging technology.
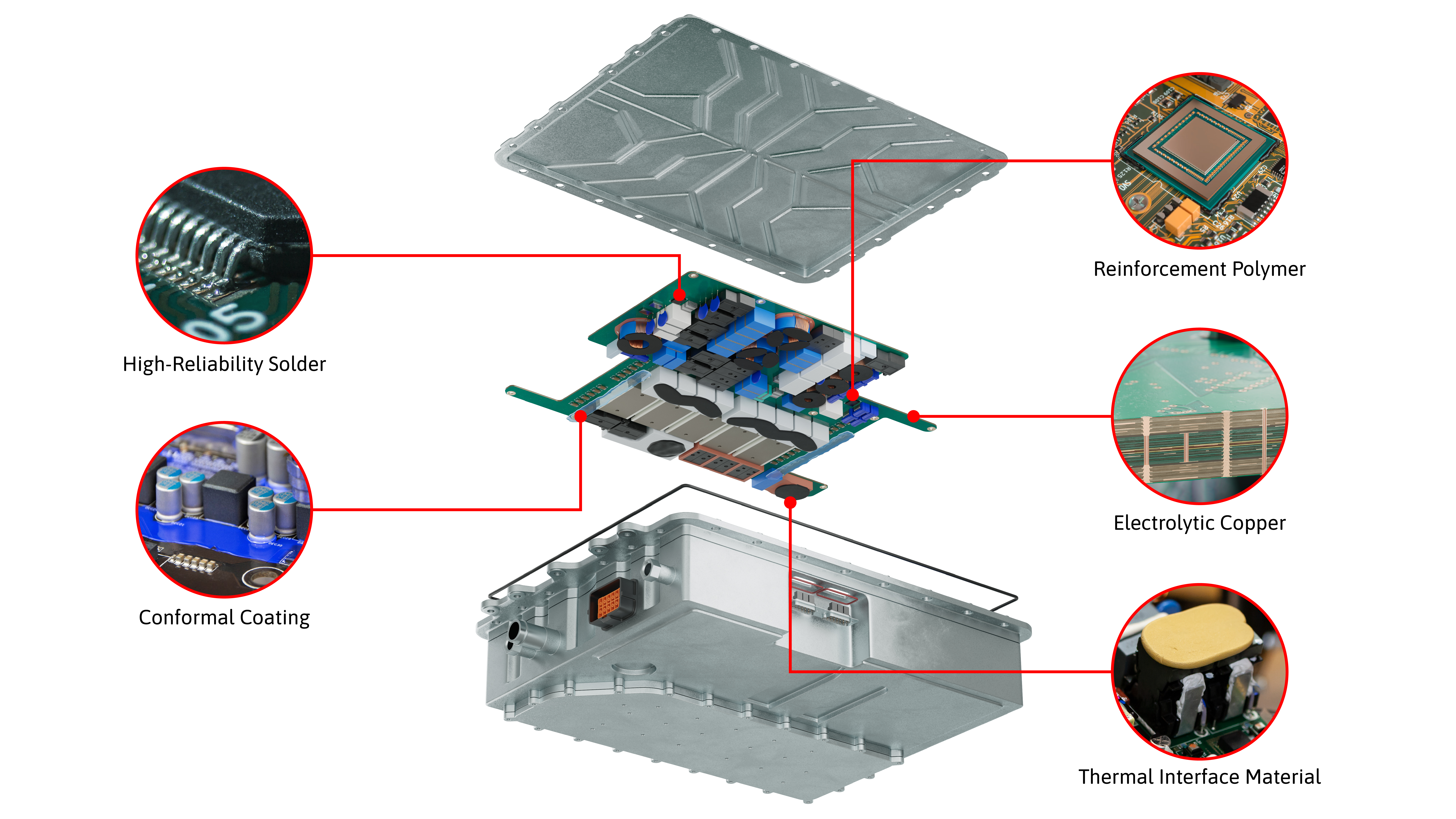
High-Performance Solder, the Key to Reliable Connections
High-reliability solder alloys, engineered to endure the extreme thermomechanical stresses inherent in high-voltage EV charging applications, are setting new standards for solder joint reliability. These advanced materials consistently outperform traditional SAC305 alloys in key reliability metrics, including high-temperature endurance, thermal cycling, vibration resistance and drop-shock durability.
One standout example is ALPHA® Innolot®, a portfolio of patented lead-free, high-reliability solder alloys. Designed for exceptional thermal cycling performance across a broad temperature range of -40oC to 150oC, these innovative solder alloys feature a refined microstructure that provides outstanding resistance to creep-fatigue stresses.
These enhanced properties boost solder joint reliability, making them ideal for connecting critical OBC components such as high-power diodes, IGBTs, and MOSFETs, temperature and voltage sensors, voltage regulators, microcontrollers.
ALPHA® Innolot® is a key component of MacDermid Alpha's integrated solutions portfolio, enabling next-generation OBC systems to achieve unmatched durability and performance. Combined with our advanced polymers, coatings, and thermal management materials, this high-reliability solder ensures seamless interconnectivity and long-term reliability for automotive electronics.
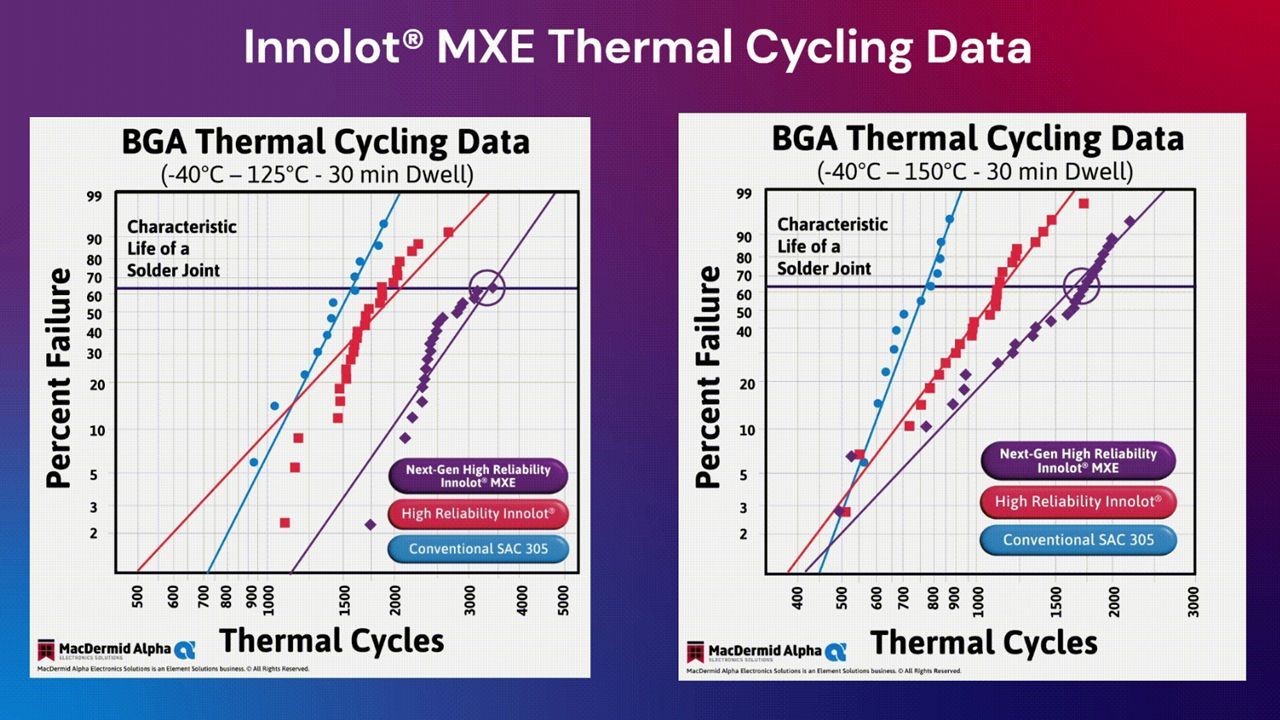
Reinforcement Polymers for Enhanced Board-Level Reliability
Reinforcement polymers extend the board-level reliability of electronic assemblies across various applications. For example, in OBCs utilizing flip-chip packages, capillary underfill is commonly employed to mitigate thermomechanical stress caused by coefficient of thermal expansion (CTE) mismatch between the component and the board.
ALPHA® HiTech® Underfills are specifically formulated for efficient capillary flow, enabling them to penetrate beneath flip-chip packages at room temperature providing robust reinforcement for on-board components. These advanced underfills have been proven to enhance the board-level reliability of critical components, ensuring durability throughout their lifecycle, even under harsh operating conditions.
ALPHA® HiTech® Underfills are a critical part of MacDermid Alpha's integrated approach to reinforcement and reliability. Designed with a high glass-transition temperature (Tg) and low CTE, these automotive-grade polymers seamlessly complement our solder and thermal management solutions to meet the stringent requirements of today’s demanding automotive industry.
The ALPHA® HiTech® product line also features edge bonding solutions and adhesives specifically engineered to reinforce and protect soldered components in the most demanding environments.
*In OBC design, strategically combining structural (polymer composite) adhesives with high-reliability solder creates a synergistic effect, dramatically boosting system reliability. By enhancing mechanical strength, thermal stability and electrical insulation, these materials form the backbone of resilient electronic assemblies. *
Thermal Interface Materials (TIMs) Optimize Heat Management
TIMs are specialized polymer composites formulated with thermally conductive fillers to meet diverse thermal management requirements. Available in forms such as pads and pastes, TIMs fill air gaps between heat-generating components and their heatsinks. They enhance thermal conductivity, facilitate heat dissipation, and prevent overheating to maintain stable operating temperatures and extend the lifespan of critical components.
In OBC design, TIMs are strategically deployed to optimize thermal management. Common placements include:
- Between heat-generating components and their heatsinks.
- Around charging connectors.
- Between the PCB and OBC chassis.
Electrolube® TIM materials accommodate varying power densities, air gap sizes, and application methods, empowering engineers to tackle the complex thermal challenges of OBCs.
The Electrolube® TIM materials are an essential element of MacDermid Alpha's integrated solutions for thermal management, working in concert with our advanced solders and conformal coatings to optimize heat dissipation and ensure the reliability of OBC systems under high-stress conditions.
Conformal Coatings Protect Circuits in the Most Extreme Environments
Conformal coatings form a thin, electrically insulating polymer layer that shields PCB electronics from dust, moisture, condensation, and corrosive gases. This protective barrier prevents system failures caused by corrosion, electrochemical migration, and dielectric breakdown.
Typically applied through selective spraying or automated dipping, these coatings protect critical components in OBC applications, including integrated circuits (ICs), resistors, and capacitors, to name a few. They also protect leads, solder joints, and PCB tracts, enhancing system reliability even in harsh environments.
Electrolube® conformal coatings are a vital component of MacDermid Alpha's integrated solutions, providing environmental protection and electrical insulation that complement our solder, TIMs, and reinforcement technologies. Together, these solutions ensure robust performance for automotive PCBs in even the harshest environments.
The Electrolube® conformal coating portfolio includes solvent-based acrylics, polyurethanes, and hybrid chemistries, as well as solvent-free options such as acylated urethanes and 2-component polyurethanes. At MacDermid Alpha, we leverage our integrated solutions expertise to recommend compatible materials for solder fluxes and conformal coatings, ensuring optimal performance and reliability.
Advanced Copper Plating for Superior Interconnectivity
The efficiency and reliability of electrical pathways within OBC circuit boards are fundamental to ensuring effective signal transmission across the device. These circuits involve intricate conductive patterns routed through multiple PCB layers, and demand precision fabrication to meet the needs of today’s modern EVs.
MacDermid Alpha’s MacuSpec™ electrolytic copper solutions deliver exceptional reliability for blind microvias, X-vias and high-aspect-ratio through-holes. By enabling the fabrication of larger, more reliable microvias, these solutions enhance the structural integrity of metallized hole walls and strengthen overall circuit integrity.
In addition to delivering outstanding interconnection quality, MacuSpec electrolytic copper solutions offer benefits such as improved metal selectivity, reduced waste, and higher manufacturing yields. These advantages help fabricators achieve sustainable production goals while addressing the high-speed, high-voltage demands of next-generation EV charging systems.
MacuSpec™ electrolytic copper solutions exemplify MacDermid Alpha's integrated approach to PCB fabrication. These advanced metallization technologies, in combination with our TIMs, solders, and protective coatings, enhance interconnectivity, durability, and sustainability for next-generation automotive PCB designs.
Collaborating with the Integrated Materials Experts
The rapid evolution of modern EVs presents significant challenges for in-vehicle electronics, particularly onboard charging systems (OBCs). Addressing these challenges requires innovative solutions to ensure thermal stability, mechanical strength, electrical insulation, environmental protection, and the capacity to manage high voltage charging.
Meeting the challenges of EV onboard chargers requires innovative materials and seamless integration. MacDermid Alpha delivers proven solutions that enhance the safety, reliability, and efficiency of OBC electronics. Reach out to us today to explore how our advanced technologies can drive your success in the evolving automotive landscape.
Let us know how we can help!