The EV Industry: China vs Rest of World - China's Distinct Culture and Technological Advancements in the Global EV Landscape
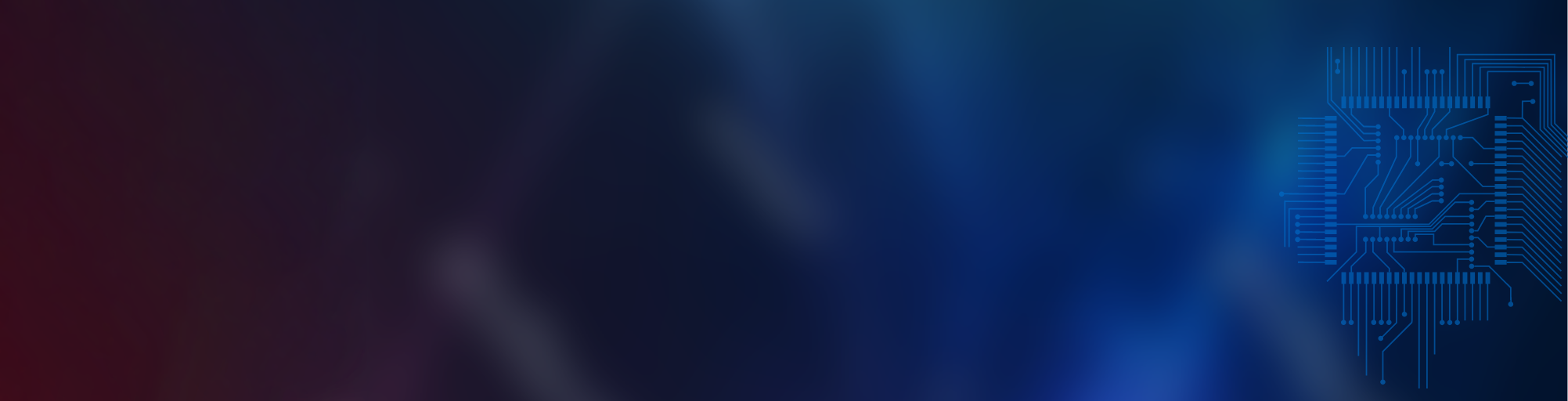
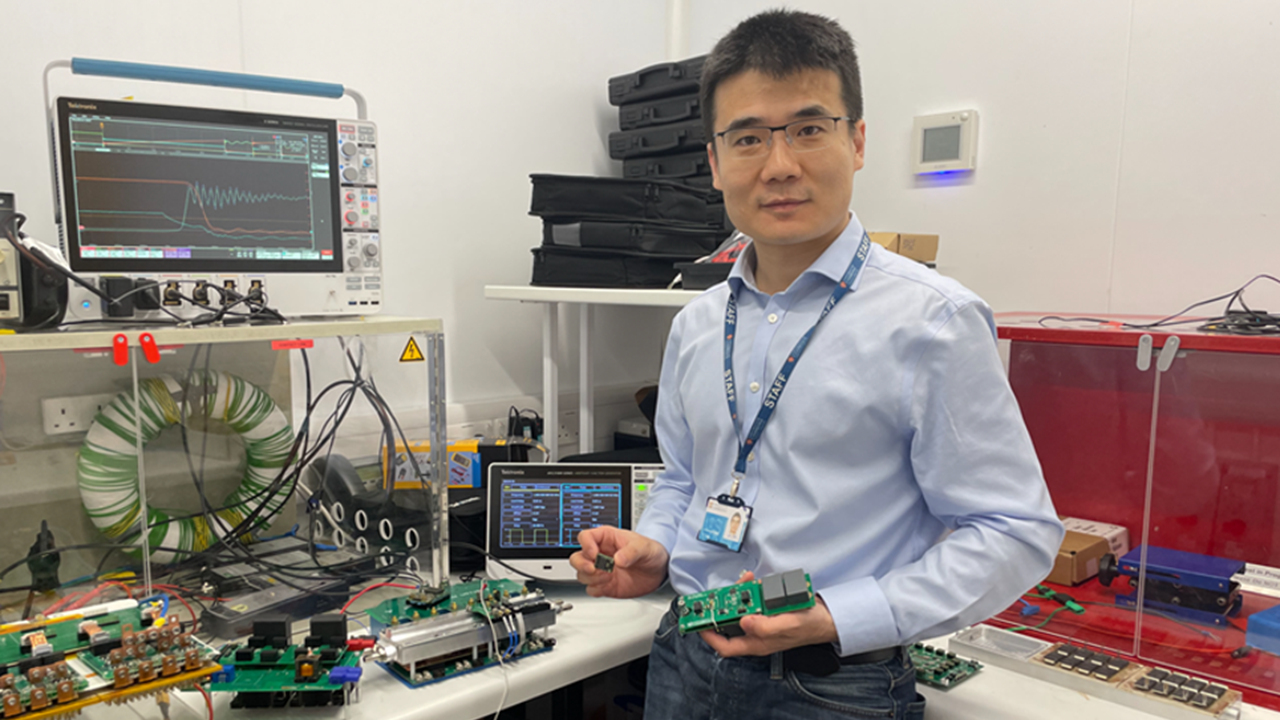
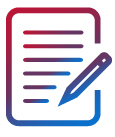
Download this Article
English Version
Simplified Chinese Version
Introduction
With rapid advancements in automotive electronics technology, the pursuit of solutions that enhance performance, reliability, and efficiency is constant.
Pioneering Technology
Silver sintering has emerged as a pioneering technology, revolutionizing the manufacturing processes within the automotive industry. Recognized for its exceptional thermal conductivity, high performance, and reliability, silver sintering is fast becoming a key method in the production of electronic components crucial to modern electric vehicles (EVs). As automotive engineers strive to meet stringent regulations and elevate vehicle safety standards, the adoption of silver sintering aligns seamlessly with these goals. This innovative technology, introduced to the market by MacDermid Alpha Electronics Solutions, not only offers enhanced thermal performance and reduced weight for EVs but also contributes to the creation of a sustainable future for automotive systems.
Professor Teng Long, Professor of Power Electronics from the Department of Engineering at the University of Cambridge, discusses China's unique approach to leading the global EV industry. This interview explores the intriguing interplay of cultures and technologies in the global EV landscape, shedding new light on how China's strategies differ from those of other countries.
What, in your opinion, are the main differences in terms of the electric vehicle (EV) market ecosystem between China and the rest of the world?
A Growing Industry
Firstly, the government initiative that includes purchase and registration of EV vehicles in China is one of the most generous in the world. Initially, there were heavy subsidies, but these have reduced over the last couple of years. So, if you look at the incentive you can get from the government in China, it is better now than in most other countries around the world. For example, according to Reuters (June 2023) a new 520-billion-yuan ($72.3 billion) package of tax breaks was announced to support purchases of electric vehicles.
The EV industry and supporting infrastructure, if we refer to the industry as a whole and not just the vehicles, also receives private investment, from both domestical and international investors. This is because transport electrification is a fast-growing industry in China, and it is a chance for either themselves or the companies they have invested in to experience growth.
Emotional Attachments
In China, people can be quite emotional in this industry, because China has been talking about making their own cars for the greater part of century. I remember when I was a teenager, people would say, “See how many cars there are now in China but there were not many you would recognize as a Chinese brand.” But now, if you look at the electric vehicles, Chinese brands such as BYD, GAC-Aion, Changan, Wuling, Li, Nio among others are compellingly well received from lines ranging from budget to luxury. This has changed the entire mindset of both Chinese people and, I think car buyers all over the world. Consumers today have environmental concerns and transitioning to EVs is seen by the car buying public to combat pollution and reduce carbon emissions.
If you look at some of the Chinese EV brands, they are now comparable in price to foreign brands but in parallel they have better performance and specifications. Chinese Tier 1 supplier such as Inovance Automotive have started providing inverters and OBCs to European OEMS. With today’s manufacturing knowledge, they will still be exceptionally good vehicles and powertrain parts. So, the trend for the Chinese to take the lead in global EVs manufacturing is highly probable.
Infrastructure
For the charging infrastructure, especially for large cities some 8 million EV chargers have been installed in China, including more than 2.5 million public chargers. This number is continuously increasing. I have no doubt that China is rolling out its EV charging infrastructure faster than any other country in the world. I see this every day. At the electric engineering division at the University of Cambridge, behind our building, there are two car parks with zero charging points. This would not be the case in China.
Embracing Modern Technology
If we look at the industry, the vehicles, the infrastructure, all the companies, investors, and the government, the enormous scale of that, from my own personal experience, having travelled and worked in different countries, it is unprecedented and very impressive.
A significant difference between the Chinese EV manufacturing supply chain, compared to EV industries around the world, is that they are more willing to take risks to adopt innovative technologies. This is quite surprising, but they have a greater willingness to embrace innovative technologies, especially in comparison to European companies, which need extended periods to adopt innovative technologies. From my perspective, the Chinese OEMs and Tier1s are more accepting of recent technologies to solve problems. To stay competitive, the Chinese companies are more prepared to take chances to gain future market share.
My Area of Expertise – Power Electronics
Conventionally OEMs have bought systems related to Power Electronics. Now Chinese OEMs are making their own traction inverter power modules, their own packaging, and have even started making their own power semiconductors and have their own fabrication! If we look even closer, the power inverters companies are now adopting silicon carbide and specify sintering as the joining technology. This is real example of embracing technological change.
So, you can see the vision and the ambition of those OEMs. In the future, they do not want to be controlled by other suppliers. In 2021, there was a global shortage of chips and a 500% price increase. This was a very unnerving time as OEMs had to wait after a customer placed an order, which led to a delay of 6–9 months to have the car delivered. Consumers do not tend to have this level of patience, and this made Chinese OEMs want to take as much control and become more ‘in-house’ to avoid such setbacks in the future.
There is also a culture of deep collaboration and joint ventures with other companies throughout the supply chain, and some companies have invested in lithium mines to compete more effectively in making battery cells. Every Chinese OEM, if they have the resources and the cash reserves, which are important to investors for R&D and manufacturing, will do everything they can to be more integrated.
You mentioned about the adoption of sintering as the joining technology for silicon carbide (SiC) semiconductors. In 2023, some 80% of the Chinese EV market is silicon IGBT. Do you see that changing (to SiC) over the next few years?
I am confident that silicon carbide will be used in half or even maybe more than half of the traction inverter market in the next 5 years. I have reached this conclusion from every large OEM in China, claiming that they already have all their new models with silicon carbide semiconductors in the EV inverter. The primary reason for this change is that OEMs use silicon carbide to save on battery costs. The SiC devices are clearly more competitive in 800V battery systems which have been adopted by Chinese EV OEMs.
By using sintered silver for attaching power semiconductors within the inverter, it allows for improvement of the thermal and electrical passthrough, offering a significant increase in reliability and efficiency. Data has shown that there is more than a 30% reduction in losses and reliability increases by twofold and can be attributed to the silver sintering used in traction inverters. These enable OEMs to design drivetrains with greater range, lighter weight, and better reliability.
Regarding joining technologies, what are the specific advantages of silver sintering compared to traditional SAC based solder joining?
Firstly, silver sintering provides lower resistance, which comes from the silver itself, giving a benefit of higher conductivity along with the lower resistance. Sintering is also thinner than solder. Silver sintering can operate at more than twice the temperature than conventional soldering. Another key factor is that sintering allows for a higher bonding force. This is a critical factor in EV powertrain reliability, particularly for facilitating SiC power electronic devices operating under a higher temperature and larger thermomechanical stress.
The only possible drawback of sintering is that the state-of-the-art sintering process still requires pressure to complete the joining aspect of the process. Still, this challenge has been overcome with the introduction of nano particle silver sintering technology. This is why it is now gaining traction, and as indicated above, heading towards the dominant joining technology in powertrain inverters.
Do you think it is enabling technology that is helping the move to silicon carbide, or is it the fact that people are moving to silicon carbide and silver sintering is the best joining technology? Is it one or the other or both?
The sintering joining technology enables SiC power devices used in high power density converter applications such as EV traction. SiC devices are more efficient and can operate at higher temperature than the silicon counterpart. However, SiC devices have higher thermomechanical stress, which requires a stronger bonding force. From this point of view, you need something that will offer a stronger, firmer hold, which is why we need sintering.
Normally, people consider silicon carbide to be better for devices because they want better cooling and for the entire system to be more advanced. To unlock this potential, we use silver sintering to improve the cooling route from the chip to the heat sink to the coolant. Silver sintering enables a superior ambient route with lower thermal systems overall, from the chip or junction to the coolant.
At the University of Cambridge, we have been working with nano silver sintering technologies from MacDermid Alpha Electronic Solutions. The silver sintering allows for a reduction in losses from the EV drivetrain, thus enabling an increase in efficiency by more than 30% compared to traditional SAC solder alloys. This has a significant impact in terms of how sintering facilitates range, reliability improvements and lightweighting advantages.
In terms of the China EV supply chain, are engineers aware of the advantages of sintering versus soldering?
It is known that sintering is a better option, but there is a learning curve of accepting the sintering process in mass production. Companies have accumulated experience and knowledge in the reflow process. The equipment and solder paste are widely available, and adding a new sintering system is just something new. Now, it is down to finding suppliers, and the largest barrier is the lack of knowledge about the sintering process itself, rather than its technological capabilities. When an OEM decides to move their technology to silver sintering, partnering with a company which has experience in the nano silver technology, a process for optimizing the component through pre-production testing and recommendations for the application equipment is vital.
What are the advantages of sintering when it comes to low-temperature and low-pressure joining?
Soldering requires an elevated temperature, which can pose a risk to the chip. Semiconductors are sensitive to high temperatures. When we talk about reflow, it is very typical to reflow several times, and this runs the risk of sabotaging devices. Silver sintering is quite different. You can sinter both sides in one go, and the temperature is lower than the reflow sintering process can also be applied to joining the large power module package to the cooling plate in addition to joining the die chip to the power module substrate. This offers additional optimization of thermal management at the power module level and increases the reliability of the inverter.
What do you think the main technology drivers are to increase the number of electric vehicles in the Chinese market?
China has an excellent supply chain for EV batteries. That is something China does not really rely on anyone else for in this area. China also has excellent electric motors, power converters, and power electronics. China has no disadvantage as the supply chain is established and they have no burden in keeping the fossil fuel automotive industry. The big drivers of continued growth include government support and private investment, the vast charging infrastructure, and the public’s confidence and acceptance of electric vehicles. I think some of the explanations I have given above demonstrate why this is now happening.
Authored By:
Teng Long, PhD
Professor of Power Electronics
Cambridge University