Meet the Pioneers of Silver Sintering Technology for the Automotive Industry
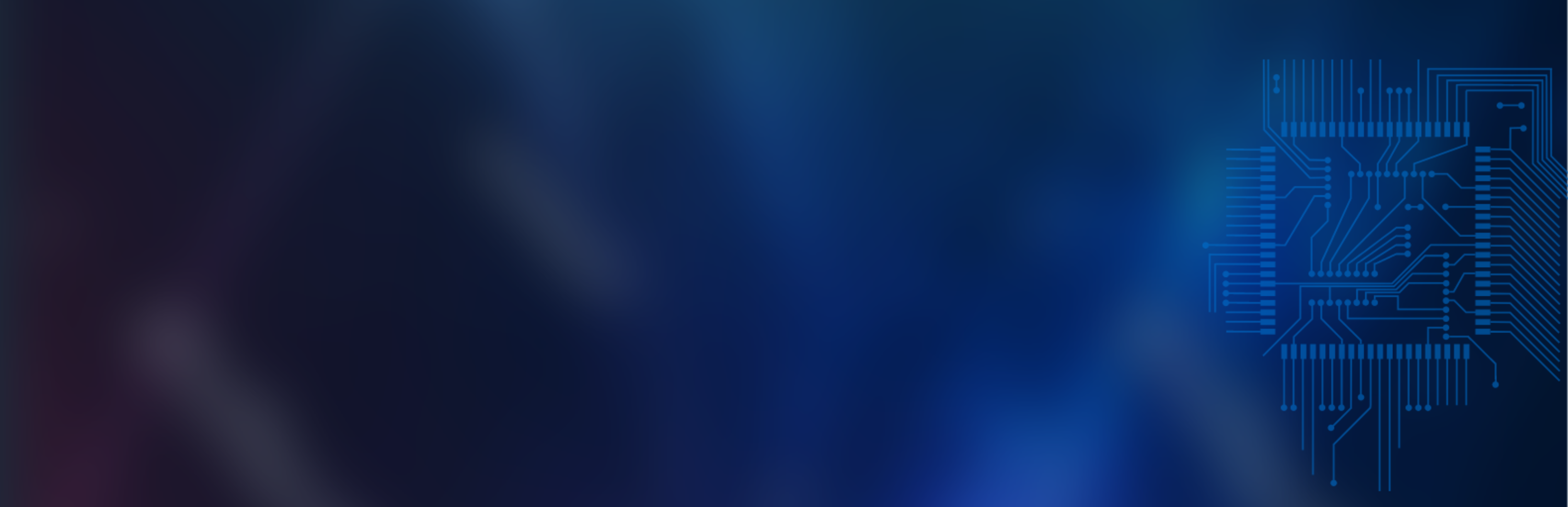
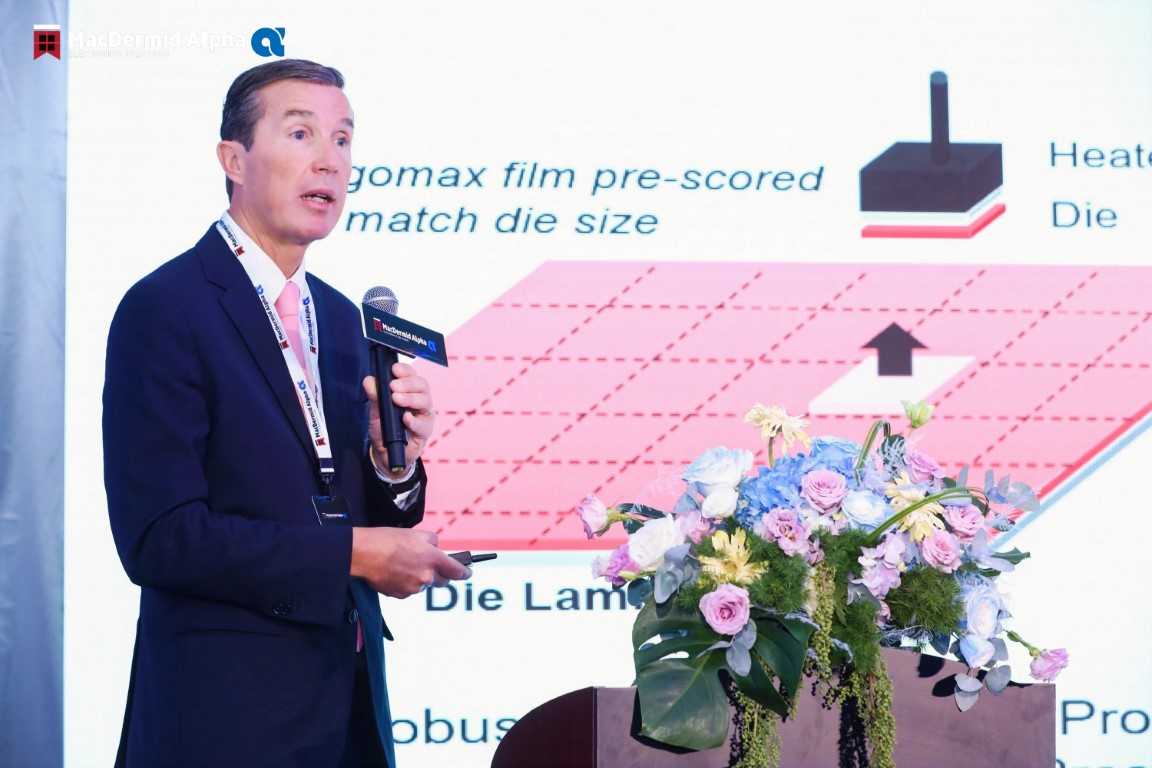
Introduction
With rapid advancements in automotive electronics technology, the pursuit of solutions that enhance performance, reliability, and efficiency is constant.
Pioneering technology
Silver sintering has emerged as a pioneering technology, revolutionizing the manufacturing processes within the automotive industry. Recognized for its exceptional thermal conductivity, high performance, and reliability, silver sintering is fast becoming a key method in the production of electronic components crucial to modern electric vehicles (EVs). As automotive engineers strive to meet stringent regulations and elevate vehicle safety standards, the adoption of silver sintering aligns seamlessly with these goals.
This innovative technology, introduced to the market by MacDermid Alpha Electronics Solutions, not only offers enhanced thermal performance and reduced weight for EVs but also contributes to the creation of a sustainable future for automotive systems.
Julien Joguet, Line of Business Director for Power Electronics, and Steve Brown, Global Director of Strategic Accounts, from MacDermid Alpha Electronics Solutions, explore the significance of silver sintering in the automotive sector, delving into its applications, benefits, and transformative impact, propelling OEMs into a new era of technological excellence.
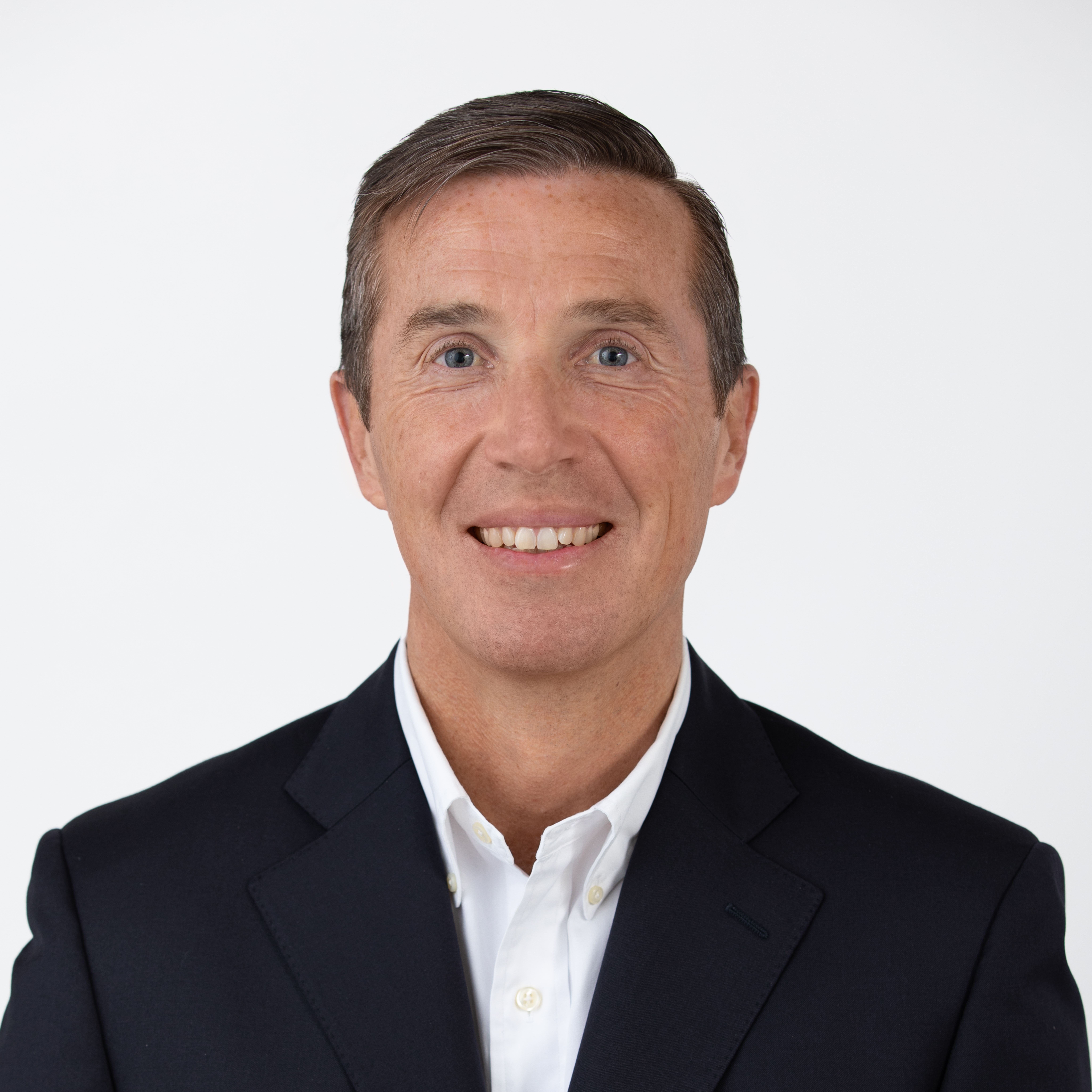
Line of Business Director for Power Electronics
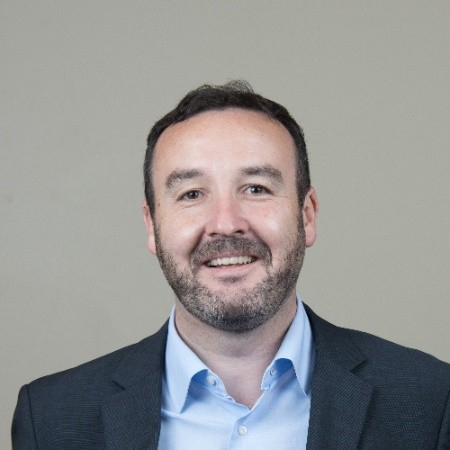
Global Director of Strategic Accounts
How did MacDermid Alpha embark on adding silver sintering to its product portfolio?
JULIEN:
We first started exploring sintering with our nano silver technology back in 2007. We were thrilled with the amazing new capabilities of silver sintering, as it enabled us to offer customers low temperatures and low pressure (sintering) over an extended period. Silver has a melting point of 962 °C, so if you want to melt silver you need to go to a very high temperature.
Low temperature
The beauty of our nano silver sinter material, Argomax®, which we launched in 2013, is that we were able to sinter at a very low temperature and process it at 200 to 250°C, which is important for die and package attach applications. We ensured that our silver sintering materials could perform within the time, temperature, and pressure that the industry required. We presented our (then) new silver sintering products at PCIM Europe, where we were able to help educate the power electronics community about sintering and its low temperature and low-pressure capabilities. A lot of interest was created at that PCIM event.
How did the market respond to silver sintering in the beginning?
JULIEN:
The first customer we had was for a very high-powered LED application. The beauty of silver in this case was that the sintering was bringing 30% more current, so this was quite remarkable. We started to sign more contracts as new power modules came to market. From this point, customers began using Argomax in high volume. That LED customer became an early adopter because they were working for German car manufacturers. These same OEMs also wanted higher reliability, a longer lifetime, and a decreased size of their power modules. Testing of the Argomax technology indicated potential for reduced weight and increased efficiency in these applications.
I remember one such meeting. We presented Argomax to a major EV manufacturer who was very interested the technology’s potential. I had film samples with me, so we could process some parts on a sinter press and show them how to apply the pressure. Two weeks later, we moved forward with the contract. They even designed their inverter around the technology and based their power module designs on our sintering process. The new technology was very impressive, and the customer was very happy.
First Time Right
The next stage in this journey was the creation of a state-of-the-art application center, which is a special silver sintering lab that demonstrates the technology and shows customers our capabilities. Primarily, we aimed to make our customers highly competitive, and we generated the motto “First Time Right”, which helped with the adoption of Argomax silver sintering. We attracted big power module customers and created the name “package attach”, which is now an industry-standard term.
So, that is how our silver-sintering capability started. We are riding through this revolution, and it’s all credit to the whole MacDermid Alpha team, as visionaries we were able to visualize the potential of this technology.
I should add a few comments on our Argomax ecosystem. Our experience is that it is critical to show customers how to implement the technology. This is why it’s not only about the product; it is about everything surrounding it as well.
Finally, another unique factor for us is that we have full control of the Argomax supply chain; this includes raw material procurement and product manufacturing. The benefit to end users is consistency and quality in supply.
How does Argomax help Power Electronic engineers optimize inverter design?
JULIEN:
The power modules were already there, sintering delivered the opportunity to produce a new, more reliable, inverter design. The overall efficiency of the car was a huge consideration; the weight, the power, the range, the technology the car is using, and the battery size all lead to calculations that show how efficient the car can be, and when you look at the top ten EVs sold and you look at their actual efficiency, it’s quite astounding to see the variations.
STEVE:
Ultimately, we can associate the performance of Argomax with the end-system, the car's performance, it’s the ultimate expression of what it does. As a materials science company, our natural position would be to talk about how much electrical or thermal conductivity it gives or how much mechanical strength it delivers.
What engineers really care about
Ultimately, what engineers really care about, if you think of it in a purer sense, is that the EV has a battery pack loaded with electronics that can convert the battery power from DC to AC and take it through to the electric motor to drive the wheels.
So, if you’ve got a system in the middle that can provide more efficient conversion of power from the battery to the electric motor, that’s a huge benefit. In theory, you can reduce the number of kilowatts out of the battery pack for the same range, or get more range from the same battery pack, or if you can take the battery pack size down, you are also reducing the weight, which also helps with range improvement. That’s what fascinates me most about Argomax: it’s the direct association with the performance of the vehicle. I think it’s very powerful.
Has silver sintering technology accelerated the adoption of Electric Vehicles?
JULIEN:
I’m sure it has. Our customers are still leading the industry because we are ahead of the pace as we offer different manufacturing options and products. Often when I am meeting with our customers and their supply chain, they remark to me just how much innovation is in our product portfolio.
STEVE:
Let me add to that. The nano silver particles of Argomax allow low temperature and low pressure sintering within a stable product. Sintering is thousands of years old; the idea of having fine powders and compressing them together to produce solid blocks of metal has been tried and tested. The revolution here is bringing it to a nascent industry (EVs) which drives their efficiency and reliability.
Why is the Alpha ecosystem beneficial for customers?
JULIEN:
Argomax Ecosystem
The ecosystem at MacDermid Alpha combines three key elements: innovation, application laboratories to demonstrate technology, and partner collaboration to show our capabilities. Bringing good products to market and being able to demonstrate them is the best possible combination, and we can see the impact of this in our Shanghai facility. It is proof that we are leading the industry. It is the best way to move forward, and that’s how we differentiate.
Argomax helps users for die and package attach
Sintering is happening, but Argomax technology helps users become much more competitive in the die and package attach space. The early adopters are clearly leading the way, with Chinese manufacturers now part of this revolution. The idea that Western brands are looking to China for inspiration was previously unheard of until now, as the technology is impressive. Car manufacturers who have not tested the technology are looking at those early adopters for design inspiration.
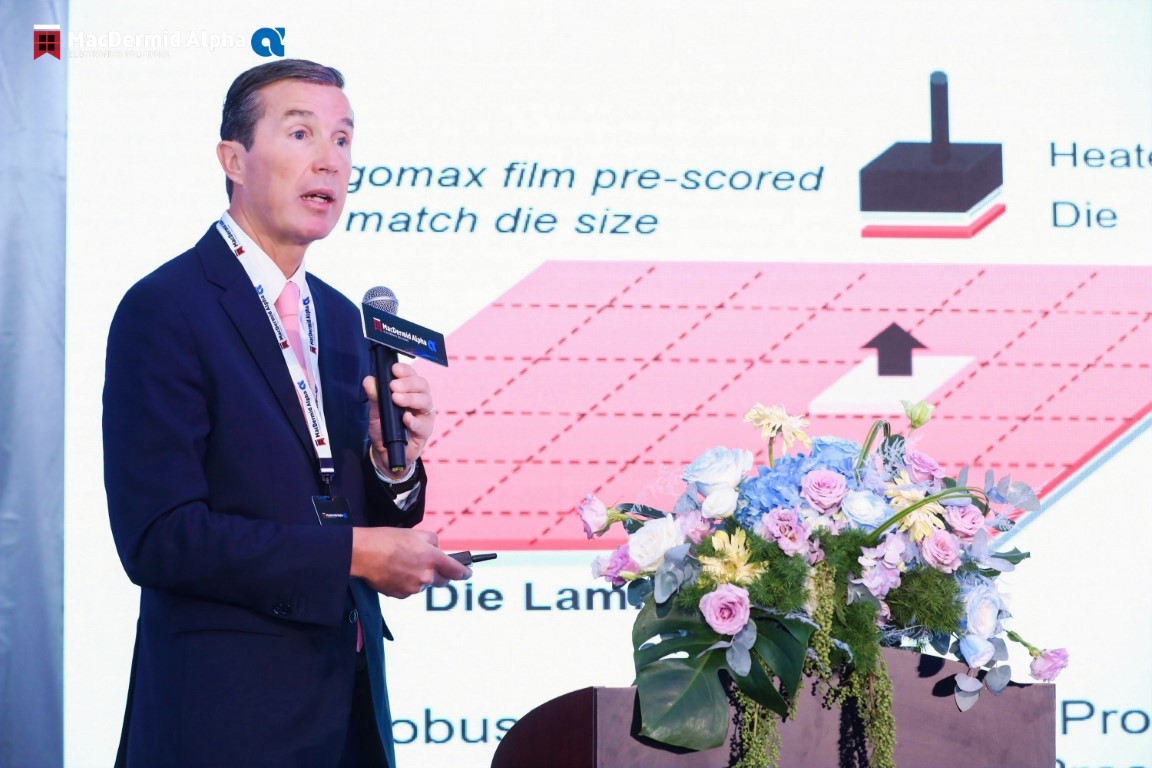
What about the bond strength of silver?
STEVE:
Strength
Once it is processed, the attachment is extremely strong. One of the key things with any joining material is that the higher the operating temperature, the closer those joints are to failure; typically, they’re in a state where cracks can propagate more freely. The difference is, of course, that with solder, you can melt it at 220 °C, and if it's operating at 130°C, you can get it within 100 degrees of its melting point, but with silver, it melts at 962 °C, so you’re never going to get close to it.
This is proven with the high-speed shear test. It’s an excellent indicator of the strength of a bond. Argomax exceeds the automotive requirements in this test. So, the stronger the bond, the more efficient the thermal cycling will be, because even if you have some cracks through a joint of any sort, if you have a very strong bond, it will survive a long period of time. With other joining technologies, it’s relatively weak, once you get a few cracks, you’ll probably get complete failure earlier.
We know that a lot of advancements have been made with Ag sintering. What do you think is next on the horizon? Copper sintering? Other materials? What does the future look like?
JULIEN:
Firstly, I think that people will look at attachment to copper as an intermediary stage. All the developments right now are being made around silver sintering. What may change is bare copper or copper plating to be able to save cost and bring some additional value to your package; that is the step in between.
ActiveCopper
Replacing silver with copper sintering is something that people are looking at to stay ahead of this trend, we recently acquired Kuprion, a developer of next-generation nano-copper technology to the semiconductor, circuit board and electronics assembly markets. The ActiveCopperTM allows us to research this technology further. Stay tuned for updates on this application.
Further information about silver sintering can be found here: Launched the China Electronic Application Center - focusing on high-end manufacturing