What is a Getter? The Unknown Component Protecting Electronics from the Inside
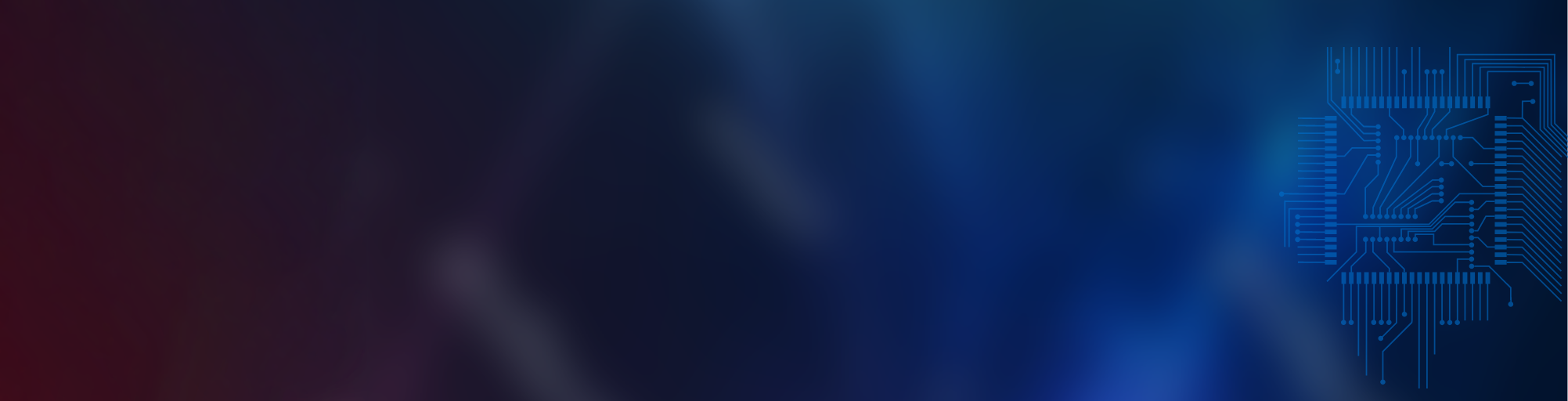
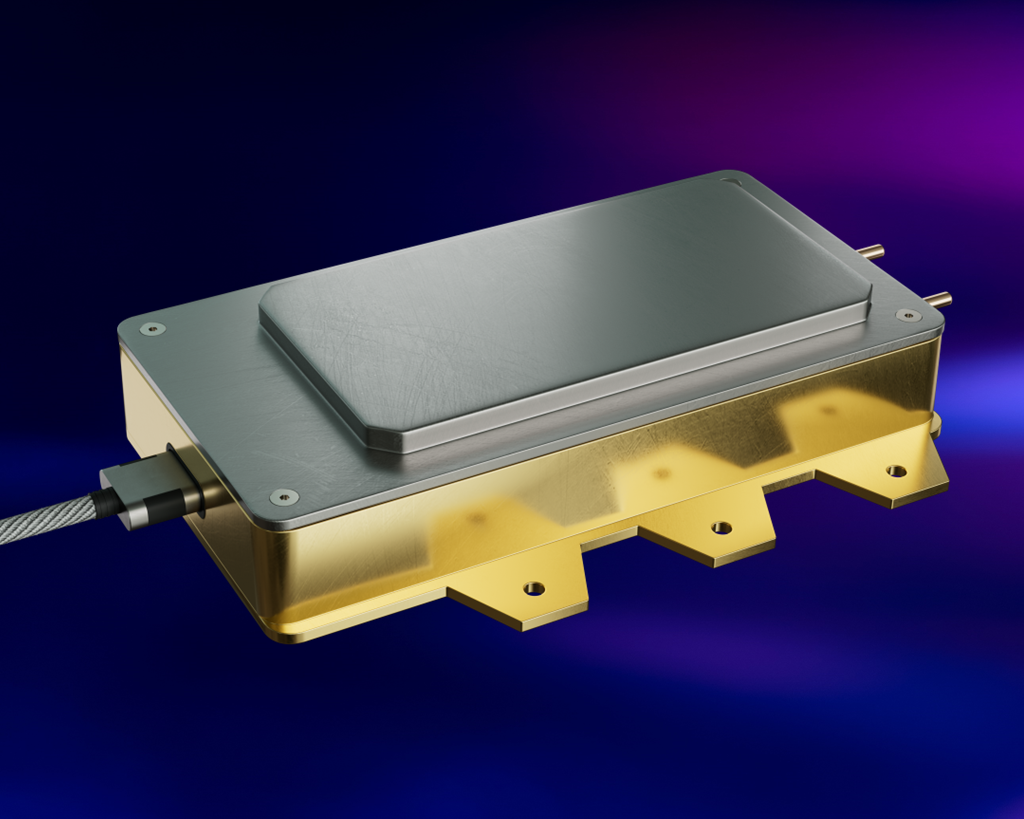
About the Author
Mike Previti
Director, Microelectronics & Sensors
MacDermid Alpha Electronics Solutions
As Director of Microelectronics & Sensors within the Semiconductor Assembly business unit, Mike has been instrumental in leading the strategic direction and growth of the microelectronics segment. Based in Suwanee, Georgia, he oversees product development and market expansion, ensuring that MacDermid Alpha’s offerings meet the evolving needs of customers in high-performance industries such as semiconductor packaging and medical devices.
Prior to his current role, Mike held various leadership positions that underscored his expertise in managing global product portfolios and his commitment to driving innovation. He has spent around 25 years in our business, where he played a critical role in supporting the semiconductor and electronics sectors. Mike's career in the field began as a Senior Research Chemist, leading research on moisture getters and underfill adhesives, a foundation that has contributed to his deep understanding of the industry.
Can you briefly explain what a "getter" is and its role in electronics manufacturing?
A getter in the electronics industry is a material or device used to maintain a vacuum or low-pressure environment by absorbing or chemically reacting with unwanted gases that might degrade the performance or reliability of an electronic component. Typically, getters are used in sealed environments like vacuum tubes, sensors, or hermetically sealed packages to ensure long-term reliability by scavenging residual gases (e.g., oxygen, hydrogen, or moisture) that could cause corrosion or other damaging effects.
How did you first encounter the use of getters in our industry?
I spent five years as Global Portfolio Manager for Microelectronics within Circuit Board Assembly, where I played a critical role in supporting the semiconductor and electronics sectors and encountered products such as STAYDRY®.
Importance of Getters
Why are getters so important for vacuum-sealed electronic components?
Getters are crucial for vacuum-sealed electronic components because they maintain the integrity of the vacuum by absorbing residual gases that can outgas from materials within the sealed environment. This helps prevent contamination, corrosion, and other issues that could compromise the performance and longevity of the components1.
Can you provide a higher-level explanation of the technical necessity of getters?
Technically, getters are essential because they ensure a stable and controlled environment within hermetic packages. They absorb gases like moisture, hydrogen, and oxygen, which can otherwise lead to oxidation, corrosion, and electrical failures. By maintaining a clean internal atmosphere, getters enhance the reliability and lifespan of sensitive electronic components1.
What kinds of problems could arise if we did not use getters in these products?
Without getters, vacuum-sealed electronic components could suffer from various issues such as moisture-induced corrosion, electrical leakage, short-circuiting, and degradation of optical components. These problems can lead to premature failure and reduced performance of the devices1.
Could you give an example of a product or technology where getters have made a big difference?
Getters have made a significant impact in the medical and aerospace industries. For instance, in medical devices like implantable sensors and pacemakers, getters help maintain a stable environment, ensuring the devices function reliably over long periods. In aerospace, getters are used in satellite components to prevent outgassing and maintain the performance of critical systems2.
Types of Getters and How They Work
Can you explain the different types of getters - non-evaporable and evaporable - and how they function?
There are two main types of getters: non-evaporable getters (NEGs) and evaporable getters (EGs). NEGs, made from materials like zirconium or titanium, absorb gases through a chemical reaction at their surface. They are activated by heating and can function over a long period. Evaporable getters, on the other hand, are typically made from barium and are used in vacuum tubes. They work by evaporating a thin film of reactive material that absorbs gases34.
How does it actually work?
Getters work by either adsorption or absorption. Adsorption involves gas molecules adhering to the surface of the getter material, while absorption involves the gas molecules being taken up into the bulk of the material. This process effectively removes unwanted gases from the sealed environment, maintaining the vacuum and protecting the electronic components4.
Are there specific materials that work best for getters, and if so, why?
Yes, materials like titanium, zirconium, and barium are commonly used for getters due to their high reactivity with gases. These materials can efficiently absorb or adsorb gases like hydrogen, oxygen, and moisture, making them ideal for maintaining a clean vacuum environment56.
Applications in Manufacturing
Which electronics products currently use getters, and how do they improve the performance or lifespan of these products?
Getters are used in a variety of electronic products, including vacuum tubes, microelectromechanical system (MEMS) devices, and optoelectronic components. They improve performance by preventing contamination and maintaining a stable internal environment, which enhances the reliability and lifespan of these products27.
How are getters incorporated during the manufacturing process?
During manufacturing, getters are typically placed inside the hermetic package before it is sealed. They may be activated by heating to ensure they are ready to absorb gases. The process involves careful handling to avoid contamination and ensure the getter material is properly positioned to maximize its effectiveness89.
Future of Getters
As electronics become more advanced, do you see the role of getters evolving?
Absolutely. As electronic devices become more sophisticated and miniaturized, the need for effective gas management within hermetic packages will only increase. Getters will continue to play a crucial role in maintaining the reliability and performance of these advanced devices1.
Are there any exciting developments or new applications for getters that we should keep an eye on?
One exciting development is the use of nanomaterials for getters, which can offer higher surface areas and improved gas absorption capabilities. Additionally, there is ongoing research into new getter materials that can target specific gases more effectively, which could open up new applications in fields like quantum computing and advanced sensors11.
Challenges and Considerations
What are the main challenges when working with getters in our manufacturing process?
One of the main challenges is ensuring the proper activation of getters, which often requires precise heating. Additionally, integrating getters into the manufacturing process without introducing contaminants can be difficult. There is also the challenge of selecting the right type of getter material for specific applications to ensure optimal performance110.
Wrapping Up
For someone who is not familiar with this technology, what is the most surprising or interesting fact about getters?
One surprising fact is that getters can significantly extend the lifespan of electronic devices by maintaining a pristine internal environment. This is crucial for applications where reliability is paramount, such as in medical implants and aerospace components1.
If there is one key takeaway you want everyone to understand about getters, what would it be?
The key takeaway is that getters are essential for ensuring the long-term reliability and performance of vacuum-sealed electronic components. They are the unsung heroes that keep our advanced technologies functioning smoothly1. Getters quietly do their job behind the scenes, ensuring that electronic components remain free from harmful gases and contaminants. Without them, many of the technologies we rely on today would not be as reliable or long-lasting1.
Acronym: MEMS microelectromechanical system (MEMS) – miniaturized devices that combine electronic and mechanical parts to detect and convert changes into electrical information.